Send A MessageWe support device customization. Please specify your material and model requirements, and we will reply to you promptly.
How to granulate organic fertilizer
Organic fertilizer granulation is the process of compressing organic fertilizer into a fixed shape through certain processing methods. The following is a detailed introduction about organic fertilizer granulation:
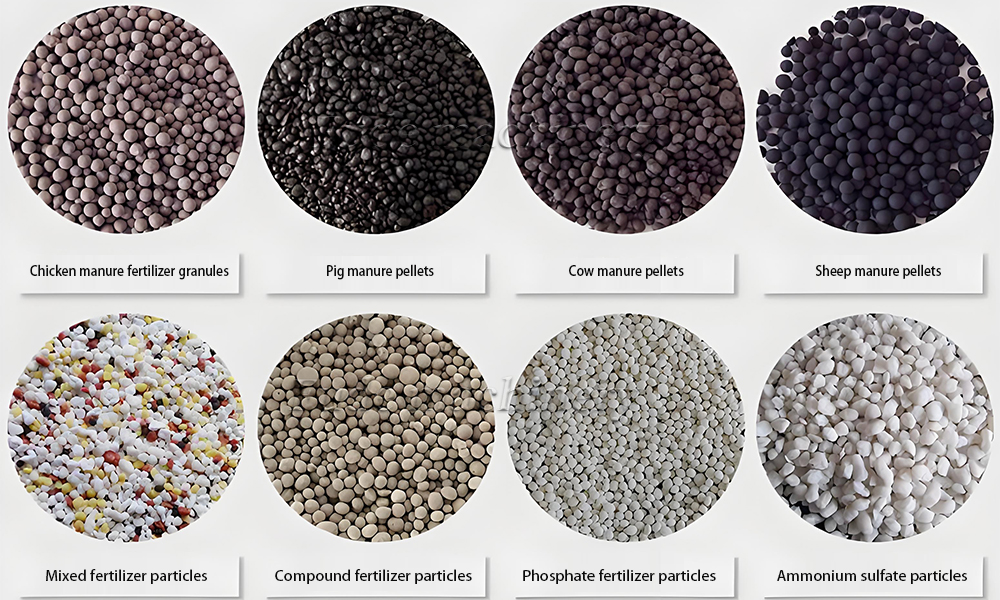
Preparation before granulation
- Raw material selection: The raw materials for organic fertilizers usually include livestock and poultry manure, crop straw, bacterial residue, etc. These raw materials need to undergo fermentation and maturation treatment to eliminate harmful substances and improve fertilizer efficiency.
- Raw material processing: The fermented and decomposed raw materials need to be crushed to achieve the required fineness for granulation. At the same time, it is necessary to mix and match nutrients such as nitrogen, phosphorus, and potassium according to the formula.
Granulation method
- There are various methods for granulation organic fertilizers, mainly including the following:
- Roller squeezing granulation method:
- Principle: Using two counter rotating rollers to squeeze the material, the air between the powder particles is expelled when the material is under pressure, and the particles are rearranged to form tightly packed particles.
- Characteristics: The generated particles have regular shapes, high surface density, and are suitable for large-scale production.
- Operation: Place the granulated powder material in the extrusion granulation equipment, and then use external force to tightly compact the powder material. Due to the different methods of external force used, the molecules are recombined to make the material appear as cylindrical particles. The entire process adopts mechanized operation.
- Stirring granulation method:
- Principle: Use agitation to mix materials, gradually causing them to aggregate into particles during the mixing process.
- Features: Easy to operate, but the generated particle shape and size may not be uniform enough.
- Disc granulation method:
- Principle: Utilizing the centrifugal force generated by the rotation of a disk, the material rolls and aggregates into particles on the disk.
- Characteristics: The generated particles have a relatively regular shape and are suitable for producing spherical particles.
Processing after granulation
- Drying: After granulation, the particles need to be dried to reduce their moisture content, improve the stability and storage of fertilizers.
- Screening: The dried particles need to be screened to remove particles that do not meet the requirements, ensuring the quality and specifications of the product.
- Packaging: The screened particles need to be packaged for storage, transportation, and sale.
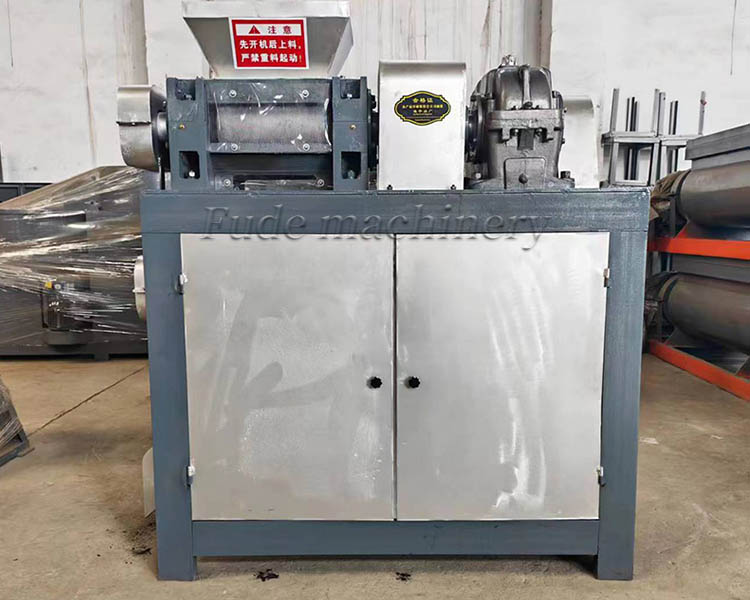
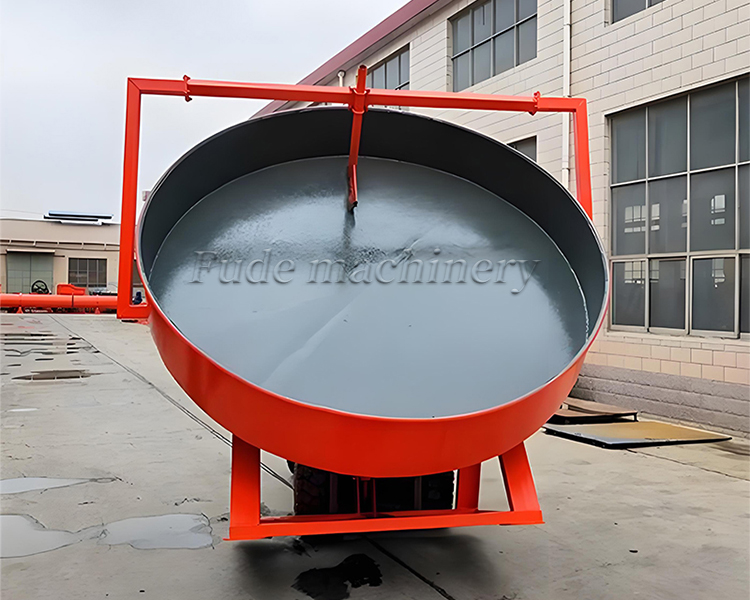
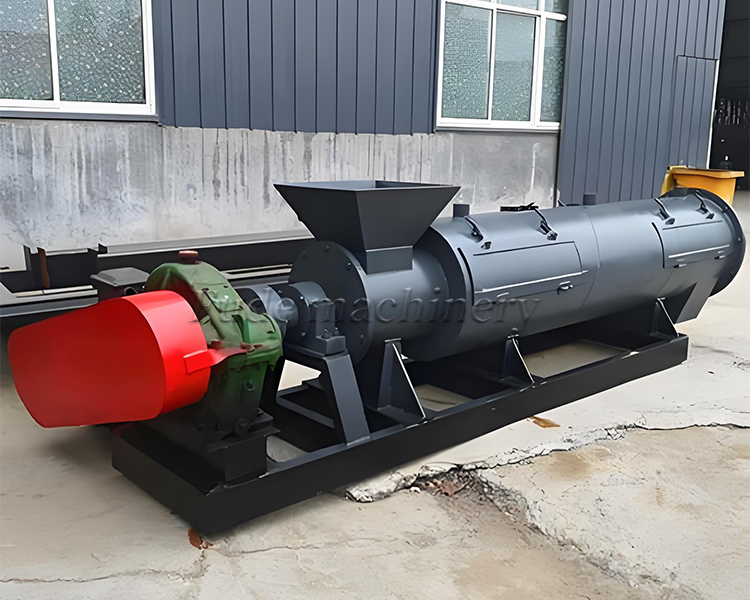