Send A MessageWe support device customization. Please specify your material and model requirements, and we will reply to you promptly.
What is the difference between a vertical crusher and a horizontal crusher
There are significant differences between vertical and horizontal crushers in multiple aspects. The following is a specific comparative analysis:
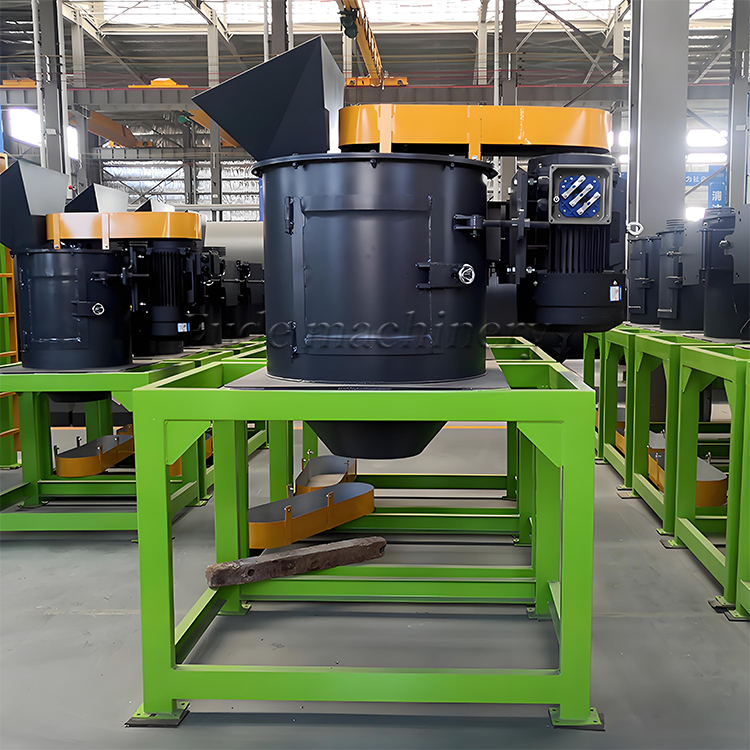
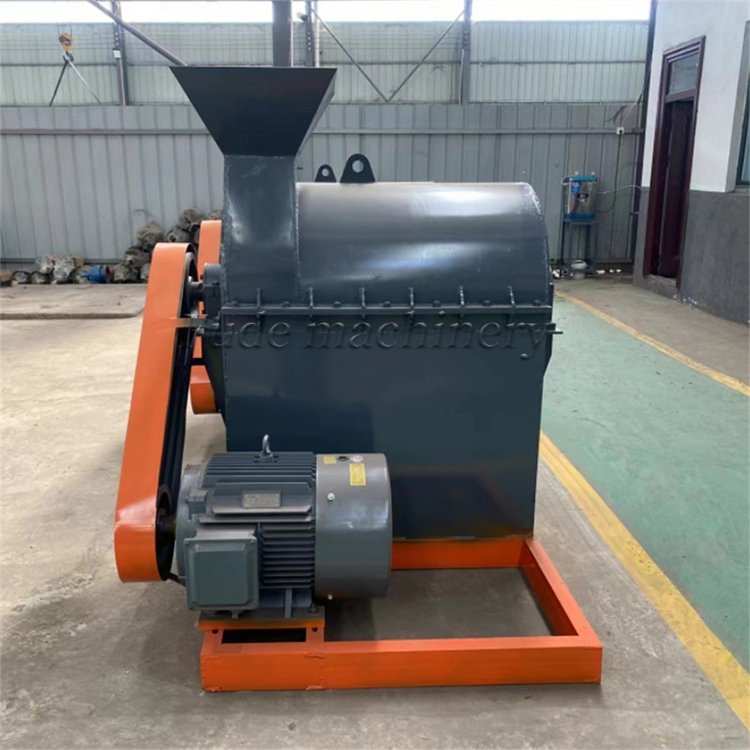
Structural differences
- Vertical crusher
- The motor is installed on the upper part, and the crushing chamber is located on the lower part.
- The material is introduced from the top and crushed before being discharged from the bottom.
- Horizontal crusher
- The motor is installed on one side, with the spindle parallel to the ground.
- The material enters from the feeding port and is crushed by a high-speed rotating spindle before being discharged from the other side.
Working principle
- Vertical crusher
- The material collides with high-speed rotating crushing components (such as hammers) inside the casing and begins to be crushed under strong impact force.
- The crushed material continues to be impacted and squeezed, gradually becoming smaller particles.
- The material is discharged from the casing through a sieve or sieve hole.
- Horizontal crusher
- The motor drives the rotor to rotate at high speed, and the material enters the crusher chamber evenly.
- The high-speed rotating hammer strikes, cuts and tears the material, causing it to be broken.
- The material is propelled by gravity from the high-speed rotating hammer head towards the baffle and sieve bar inside the frame. Materials larger than the sieve hole size continue to be hit and ground by the hammer until they are crushed to the desired particle size before being discharged from the machine.
Performance characteristics
- Vertical crusher
- High crushing efficiency, materials can be crushed finer through multiple collisions and friction.
- The power is relatively high because the crushing chamber is relatively large and requires a high-power motor to drive.
- Suitable for crushing materials with low hardness and low specific gravity.
- Small footprint, but high requirements for upward space.
- Horizontal crusher
- The crushing efficiency is relatively low, but the machine structure makes the particle size distribution of the crushed material more uniform.
- The power is relatively small, but due to limitations in the crushing chamber, it is unable to process large and harder materials.
- Suitable for crushing materials with high hardness and high specific gravity.
- The land area is relatively large, but the requirements for upward space are relatively small.
Applicable scenarios
- Vertical crusher
- More suitable for occasions with high requirements for material fineness.
- Suitable for processing materials with relatively low moisture content, such as free acid 5% calcium phosphate fertilizer.
- Horizontal crusher
- More suitable for situations where uniform particle size distribution is required for materials.
- Suitable for handling materials of various hardness, but it is important to note that the size and hardness of the materials should be within the equipment’s tolerance range.