Send A MessageWe support device customization. Please specify your material and model requirements, and we will reply to you promptly.
How do you manufacture organic fertilizer
The production of organic fertilizers involves multiple steps such as raw material selection, pretreatment, fermentation, granulation, drying, cooling, screening, and packaging. The following is a detailed organic fertilizer production process:
Raw material selection and pretreatment
- Raw material selection: Choose livestock and poultry manure, agricultural waste (such as crop straw, weeds, etc.), kitchen waste, etc. from regular breeding farms as raw materials. These raw materials should be pollution-free, free of impurities, and contain a high level of organic matter.
- Preprocessing: Crushing and screening of raw materials to remove impurities and large substances, ensuring the homogeneity of the materials. This step provides a solid foundation for the subsequent fermentation process.
fermentation process
- Mixing and stacking: Mix the pre treated raw materials evenly in a certain proportion, and then stack them into a pile of a certain shape and size. The height, width, and length of the pile should be determined based on the type of raw materials, fermentation conditions, and production equipment.
- Adjust fermentation conditions: By adding fermentation agents (such as microbial agents) and adjusting appropriate fermentation conditions (such as temperature, humidity, ventilation, etc.), promote rapid microbial growth and organic matter decomposition. Generally speaking, the suitable temperature for organic fertilizer fermentation is 55 ℃ -65 ℃, and the humidity is 50% -60%.
- Pile flipping and monitoring: During the fermentation process, it is necessary to regularly flip the pile to provide sufficient oxygen supply, and monitor changes in the temperature, humidity, and odor of the pile. The number of flips should not be too many to avoid affecting the fermentation effect. Generally speaking, the fermentation time for livestock and poultry manure is around 20-30 days.
Granulation and drying
- Granulation: Fermented materials need to be granulated by a granulator to produce uniform granular organic fertilizer. The granulation process can improve the stability and ease of application of fertilizers.
- Drying: Granular organic fertilizers need to be dried using a dryer to reduce moisture content and ensure product stability and quality. Dried fertilizers are easier to store and transport.
Cooling, screening, and packaging
- Cooling: The dried granular organic fertilizer needs to be cooled by a cooling machine to prevent damage to packaging materials or affect product quality due to excessive temperature during the packaging process.
- Screening: The cooled fertilizer needs to be screened by a screening machine to remove unqualified particles and ensure product quality. The screening process can also classify fertilizers according to customer needs.
- Packaging: The granular organic fertilizer is packaged using an automated packaging machine to form the final product. The packaging process should ensure good product sealing to prevent moisture and contamination.
Quality Control and Testing
- Nutrient testing: The completed organic fertilizer should undergo nutrient testing, including the content of organic matter, nitrogen, phosphorus, potassium and other major nutrients. Ensure that the nutrient content of organic fertilizers meets relevant standards and can meet the growth needs of crops.
- Harmful substance detection: detecting the content of harmful substances in organic fertilizers, such as heavy metals, antibiotics, pesticide residues, etc. If these substances exceed the standard, they will cause serious harm to soil and crops. Therefore, the content of harmful substances should be strictly controlled to ensure the safety of organic fertilizers.
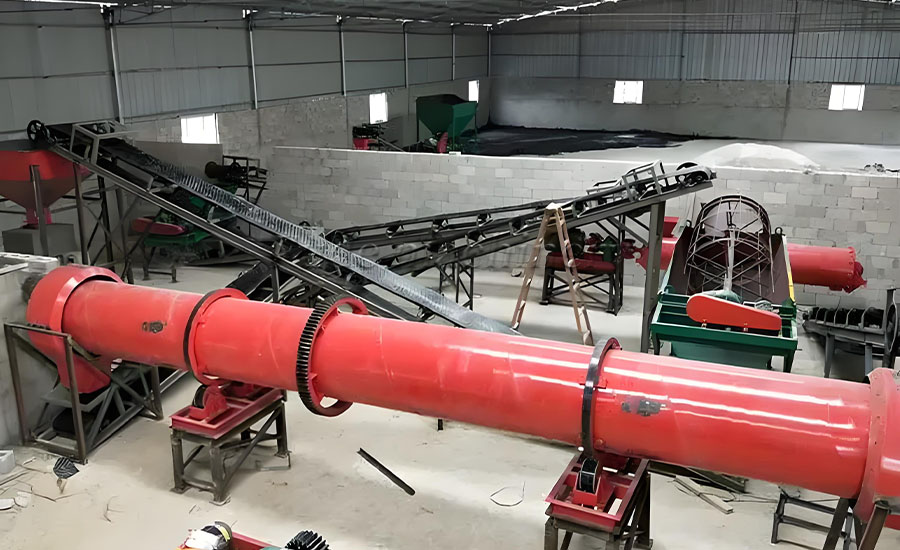