How does a granulator work
Organic fertilizer granulator is a specialized machine equipment used for producing organic fertilizers. Its working principle mainly involves multiple steps such as raw material processing, mixing, granulation, drying, and cooling. The following is a detailed workflow:
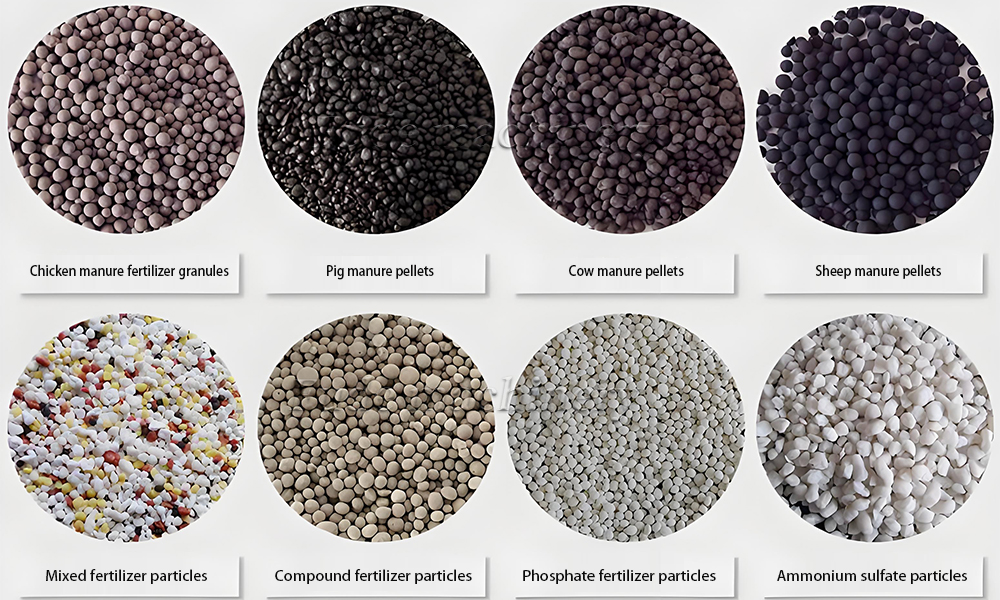
Using materials
material processing
- Raw material selection: The main raw materials required for organic fertilizer granulators are various organic waste, crop straw, livestock manure, etc.
- Preliminary processing: Clean, screen, and crush the raw materials to ensure their quality and particle size meet the requirements, and to ensure the smooth progress of subsequent process steps.
Mixing and regulating moisture
- Mixing: Mixing different types of raw materials in a certain proportion to meet the standards for making organic fertilizers.
- Adjust moisture: Adjust the humidity of the raw materials to ensure their suitability for subsequent granulation processes. This step is crucial for the granulation effect.
Granulation
- Granulation process: The mixed raw materials are pressed into granules through the mold of the granulator. The shape and size of the mold can be adjusted as needed. During the pressing process, cellulose and hemicellulose in the raw materials will be destroyed to facilitate subsequent microbial decomposition.
- Granulation type: Depending on the different types of granulators (such as disc type, drum type, vertical type, etc.), the shape and particle size of the produced particles will also vary. But overall, the granulation process compresses the raw materials into granules through the action of mechanical force.
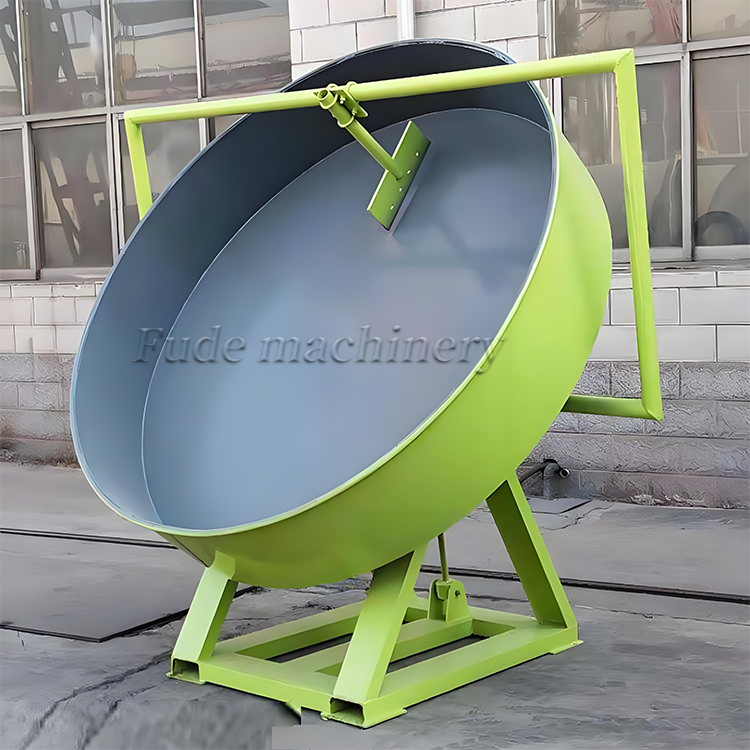
Disc Pelletizer
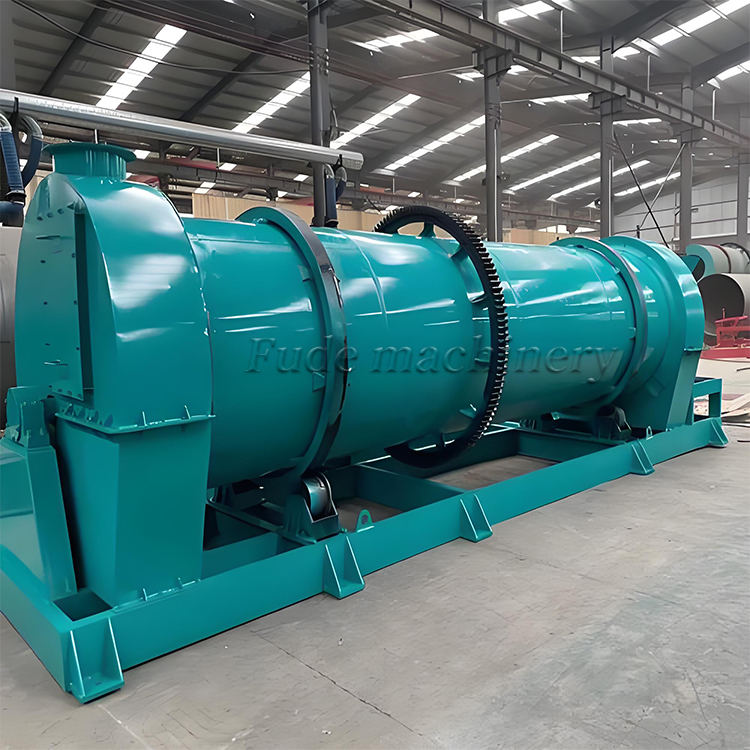
Compound fertilizer granulato
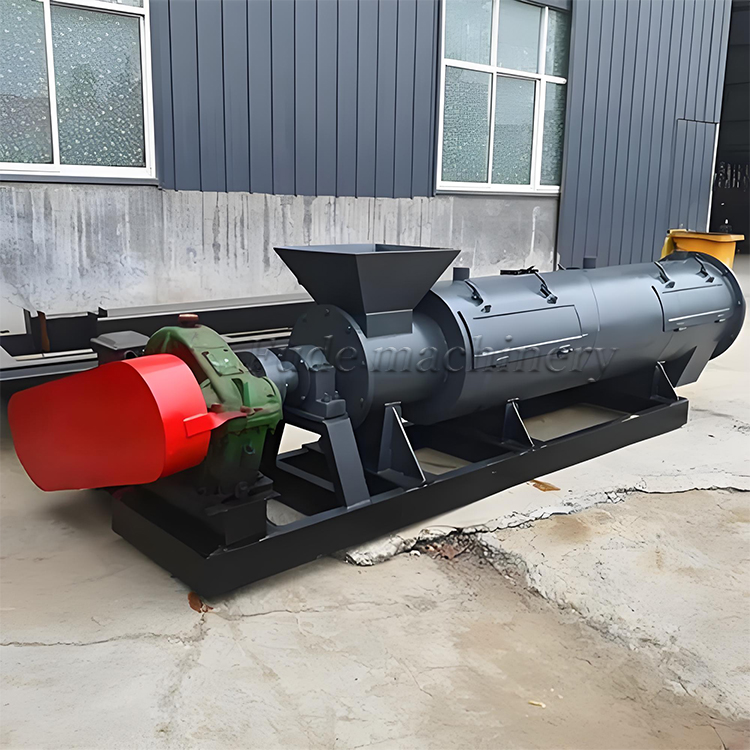
Stirring toothed granulator
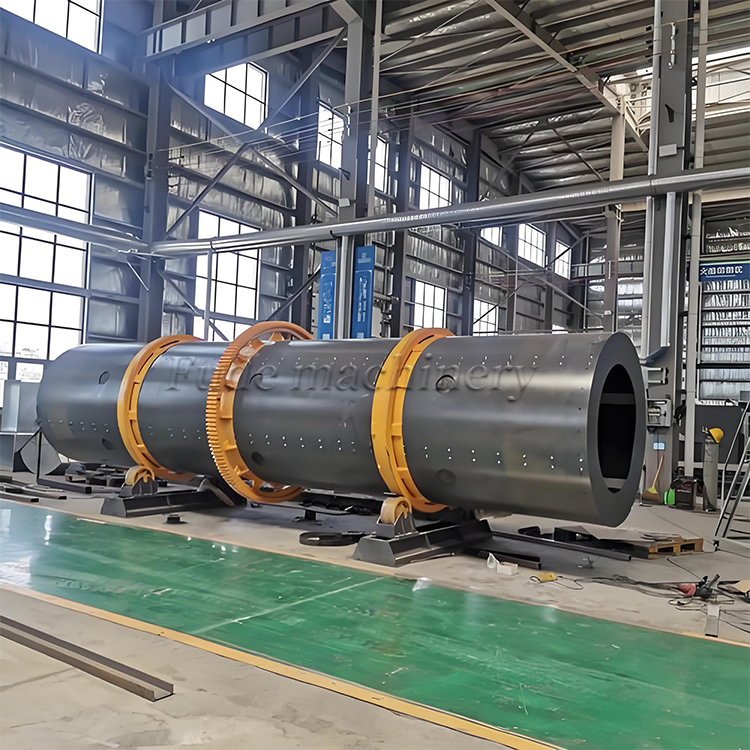
Rotary Drum Granulator
Drying and Cooling
- Drying: Place the processed organic fertilizer particles in a well ventilated area or dry them using specialized drying equipment to reduce moisture content, improve fertilizer stability and shelf life.
- Cooling: The dried organic fertilizer particles are cooled by a cooling device for subsequent packaging and storage.
Screening and packaging
The organic fertilizer particles that have been dried and cooled need to be screened to remove particles that do not meet the standards, and then packaged and sold.
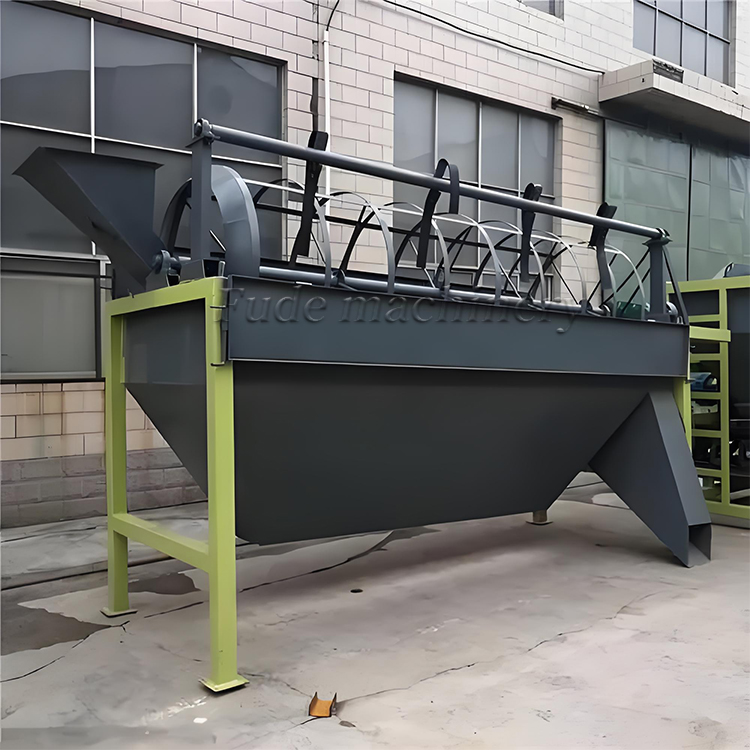
screening machine
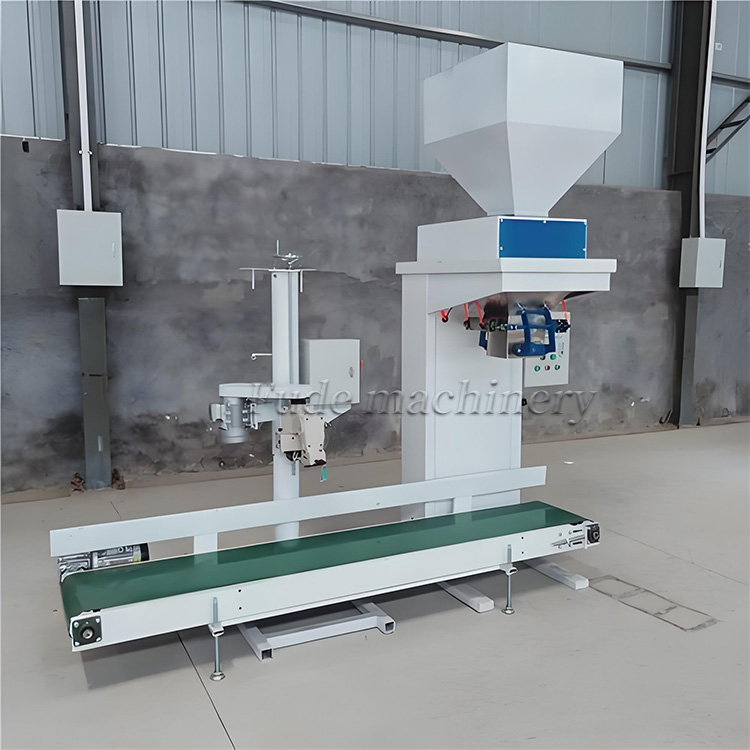
packer
maintenance
In order to ensure the normal operation and prolong the service life of the organic fertilizer granulator, regular maintenance and upkeep are necessary. This includes checking whether the various components of the machine are working properly, replacing worn parts in a timely manner, and maintaining good lubrication.
In summary, the organic fertilizer granulator converts organic waste into high-quality granular organic fertilizer through a series of complex process steps. The application of this machine not only improves the utilization rate and quality of organic fertilizers, but also promotes the sustainable development of agriculture.
Introduction to Fude Machinery Company
The production equipment includes: fermentation rake, dryer, granulator, crusher, mixer, round throwing machine, organic fertilizer production line, etc. The company will continue to adhere to the business philosophy of “quality first, customer first” and provide higher quality organic fertilizer equipment solutions for global customers.
Since its establishment in 2015, Fude Machinery has been committed to providing high-quality and high-performance wood equipment solutions to global customers. With advanced production technology, strict quality control, and continuous innovative research and development capabilities, we have received customer satisfaction praise.