What are the steps in organic fertilizer production
The production process of organic fertilizer is a complex and systematic process, mainly including the following key steps:
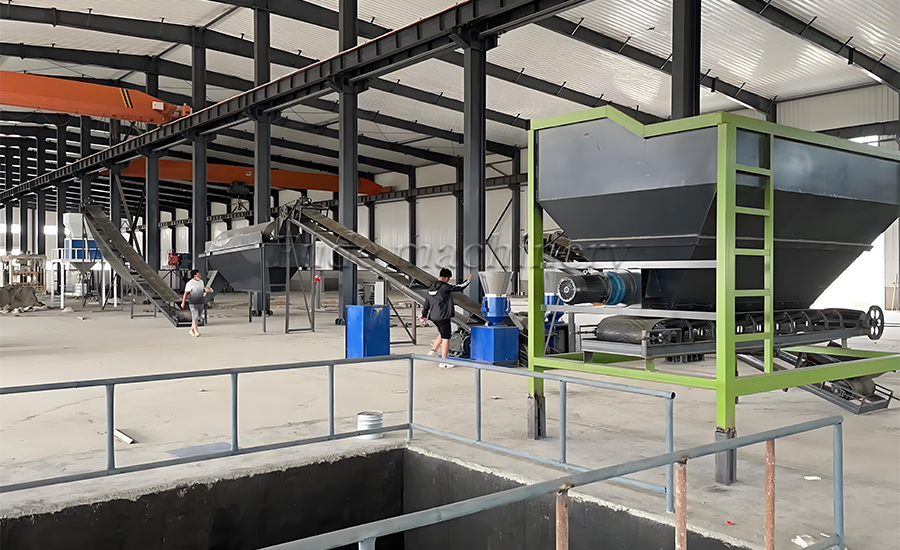
Organic fertilizer production line
Pre treatment of organic fertilizer production
- Raw material preparation: Collect and prepare the raw materials required for the production of organic fertilizers, such as livestock and poultry manure (such as cow manure, duck manure, etc.), plant straw, mushroom residue, mushroom residue, etc. These raw materials need to meet certain quality requirements, such as freshness, no impurities, etc.
- Raw material ratio: Mix different raw materials in a certain proportion according to the production process and product requirements. For example, raw materials such as cow manure, duck manure, and bacterial residue can be mixed in a certain proportion to improve the efficiency and quality of organic fertilizers.
- Mixing and stirring: Send the well proportioned raw materials into the mixing and stirring device for thorough stirring, so that various raw materials are mixed evenly. During the stirring process, an appropriate amount of water can be added to adjust the humidity and carbon nitrogen ratio of the raw materials.
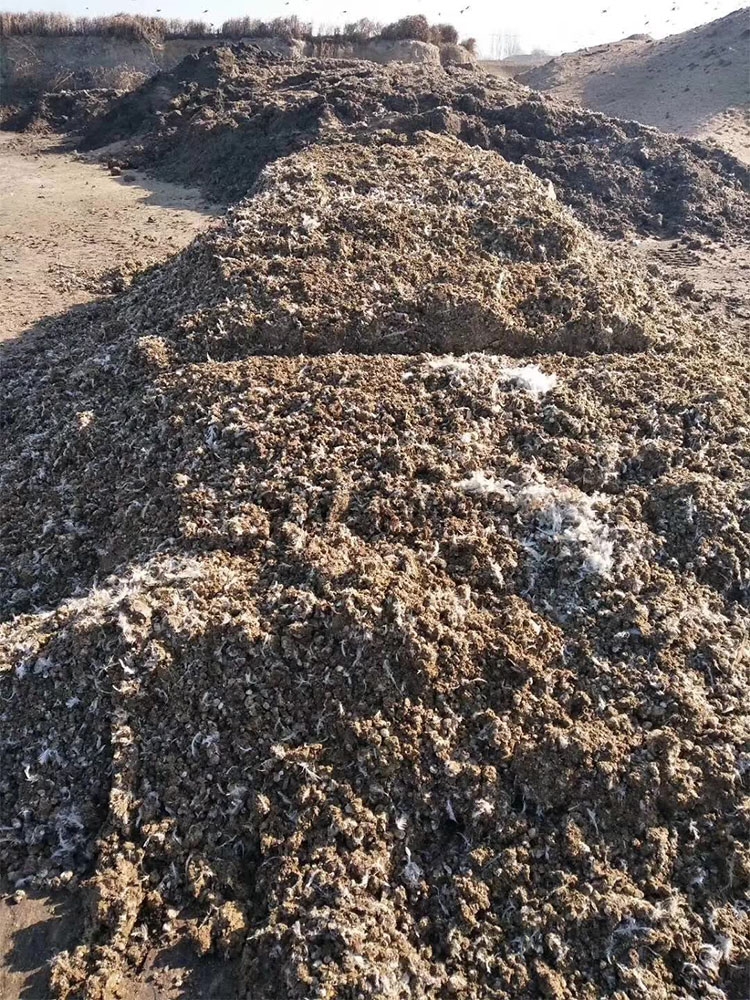
animal manure

Waste straw
primary fermentation
- Stacking fermentation: The mixed raw materials are stacked into a fermentation pile, and the height and width of the pile need to be adjusted according to the production process and equipment requirements. During the stacking process, attention should be paid to maintaining the looseness and breathability of the raw materials to facilitate the fermentation process.
- Temperature control: During the fermentation process, it is necessary to closely monitor the temperature changes of the heap. By implementing measures such as flipping and replenishing water, the fermentation temperature is controlled within an appropriate range (usually 50 ℃~65 ℃) to promote microbial growth and organic matter decomposition.
- Flipping: It is necessary to flip the fermentation pile at regular intervals (such as 2-3 days). Flipping can break the anaerobic environment inside the pile, promote the proliferation of aerobic microorganisms, and facilitate the rapid decomposition of organic matter.
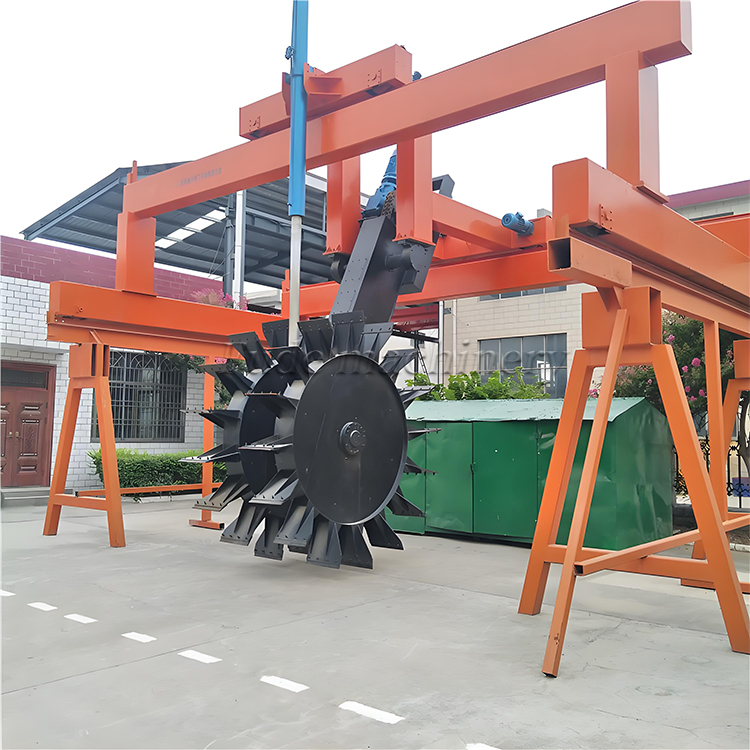
Wheel type flipping machine

Chain plate flipping machine
Post processing
- Screening: After fermentation, the fermented material is screened and processed. Screening can remove large particle impurities and incompletely decomposed organic matter from materials, improving the purity of organic fertilizers.
- Granulation: The screened material is sent to the granulator for granulation treatment. According to different production needs and raw material characteristics, different granulators (such as disc granulators, extrusion granulators, etc.) can be selected for granulation. The organic fertilizer particles after granulation have uniform size and regular shape, making them easy to store and transport.
- Drying and cooling: Send the granulated organic fertilizer particles into a dryer for drying treatment to reduce their moisture content below the standard (usually below 20%). After drying, the organic fertilizer particles are cooled to room temperature by a cooling machine to prevent clumping and deterioration.
- Packaging and storage: Quantitatively package the dried and cooled organic fertilizer particles and send them to the finished product warehouse for storage and sale. During the packaging process, attention should be paid to checking whether the particle size, moisture content, and other indicators of the organic fertilizer meet the standard requirements.
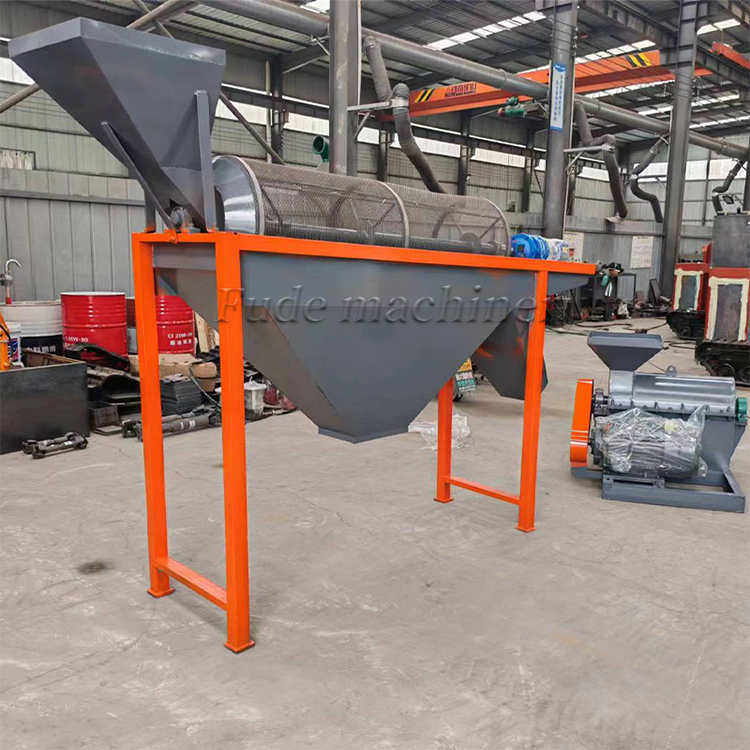
rotary sieve
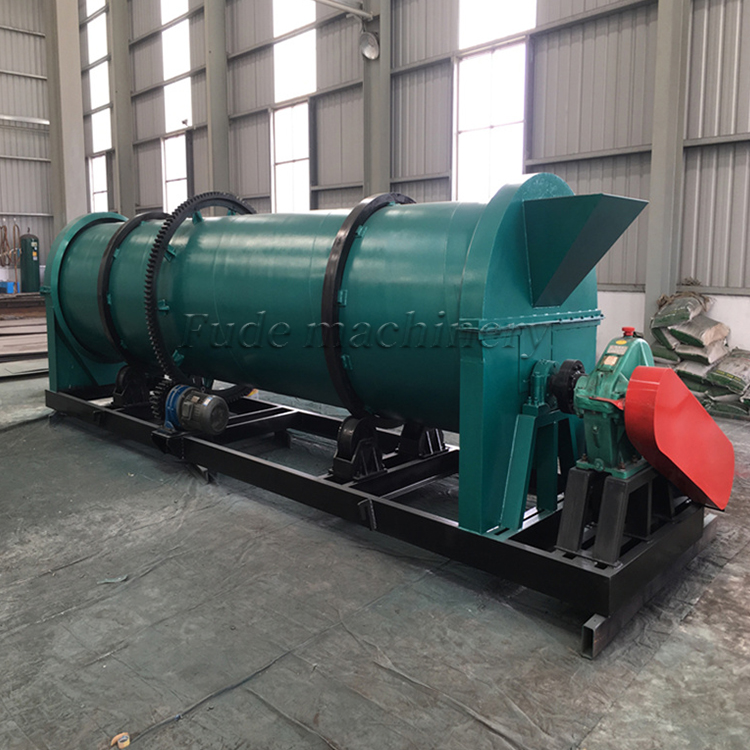
Granulators
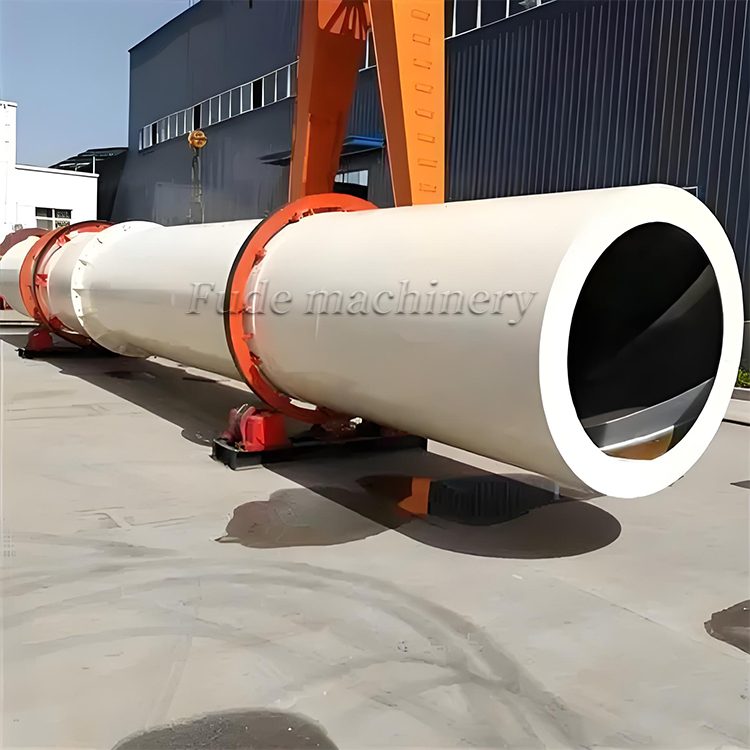
dryer
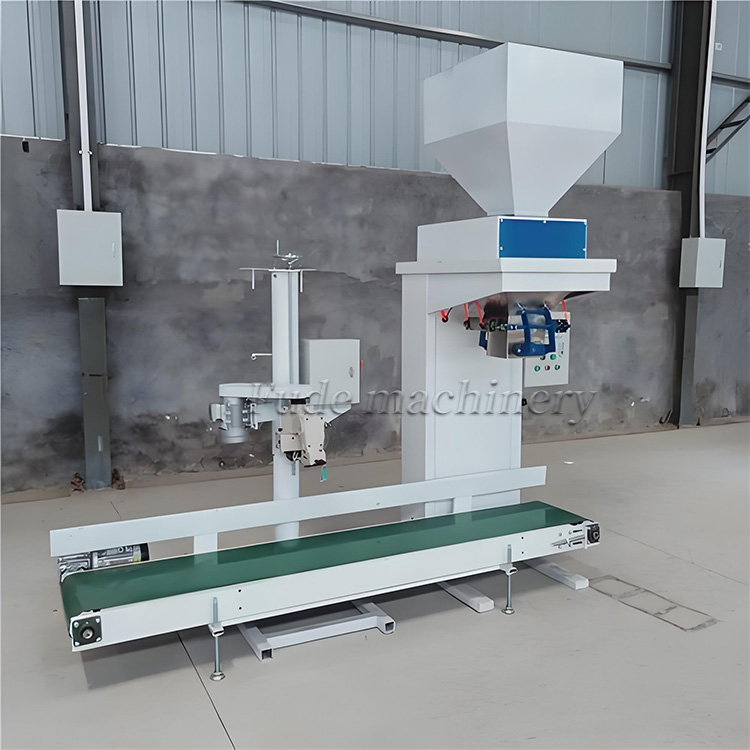
packer
Other precautions
- Raw material selection and pretreatment: When selecting raw materials, attention should be paid to their freshness and non polluting properties; During the preprocessing process, it is necessary to crush and remove impurities from the raw materials to improve the processing efficiency of subsequent processes.
- Fermentation process management: During the fermentation process, close attention should be paid to changes in the temperature, humidity, and odor of the heap, and fermentation conditions should be adjusted in a timely manner; At the same time, attention should be paid to preventing anaerobic phenomena and the accumulation of harmful substances inside the reactor.
- Product testing and quality control: In the production process of organic fertilizers, regular quality testing and control of the products should be carried out; Ensure that all indicators of the product comply with national standards and customer requirements; For non-conforming products, timely handling and improvement should be carried out.
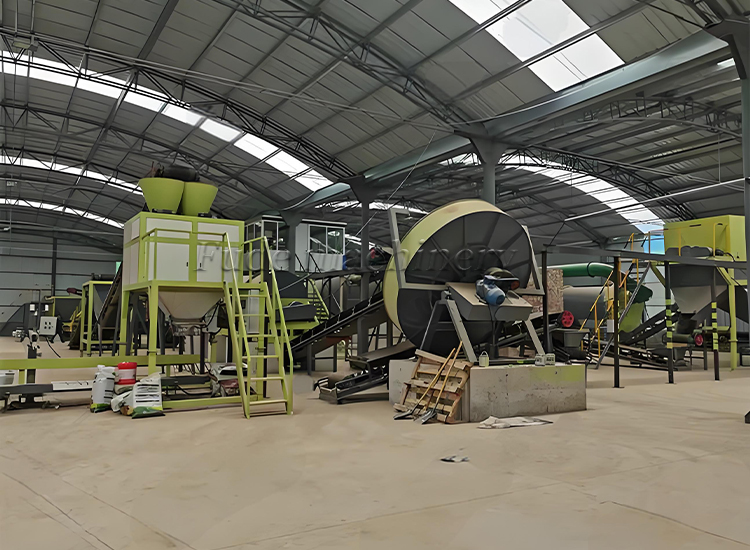
Organic fertilizer granule production line
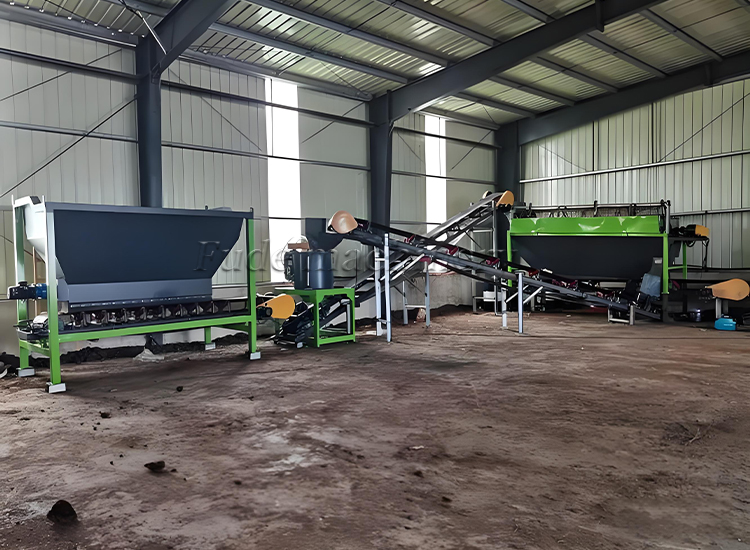
Organic fertilizer powder production line
Introduction to Fude Machinery Company
The production equipment includes: fermentation rake, dryer, granulator, crusher, mixer, round throwing machine, organic fertilizer production line, etc. The company will continue to adhere to the business philosophy of “quality first, customer first” and provide higher quality organic fertilizer equipment solutions for global customers.
Since its establishment in 2015, Fude Machinery has been committed to providing high-quality and high-performance wood equipment solutions to global customers. With advanced production technology, strict quality control, and continuous innovative research and development capabilities, we have received customer satisfaction praise.