Send A MessageWe support device customization. Please specify your material and model requirements, and we will reply to you promptly.
What is the working principle of the roller granulator
The working principle of the roller granulator mainly involves two main processes: material extrusion and granulation. The detailed explanation is as follows:
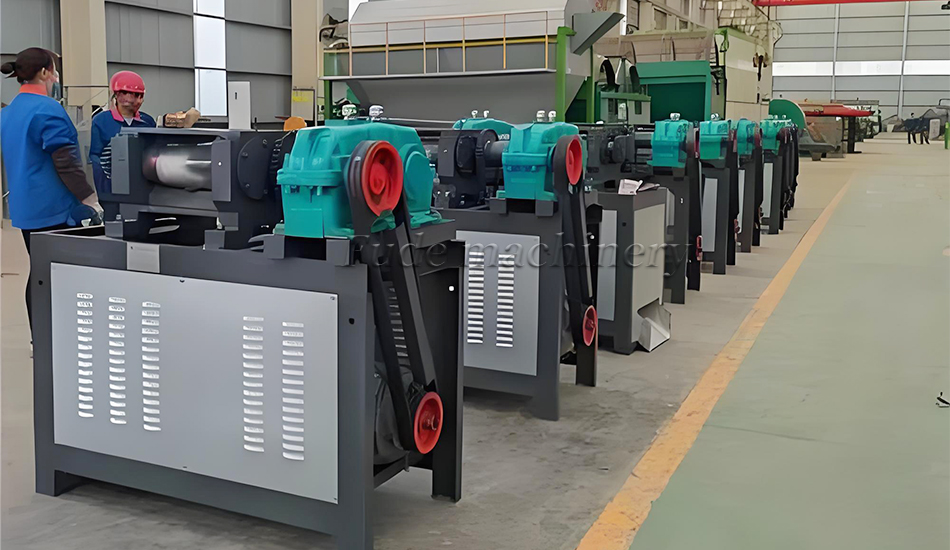
Overview of Working Principle
The roller granulator uses two relatively rotating rollers to extrude the material, causing it to aggregate into dense and hard large blocks (cakes) under pressure. This process is called the extrusion process. Subsequently, these cakes are further crushed and screened to form granular products, a process called granulation.
Specific work steps
- The material should be in powder form and the moisture content should be controlled within a certain range (usually not greater than 15%) to ensure the extrusion effect.
- The materials are added from the feeding hopper and undergo preliminary mixing and conditioning through a mixer or feeding device.
- The material enters between two relatively rotating rollers.
- The surface of the rolling mill usually has uniformly arranged hemispherical concave models or regularly arranged cavities to increase the extrusion effect and assist in forming.
- The rolling mill rotates relative to each other, applying pressure to the material, causing it to agglomerate into dense and hard chunks (cakes).
- During the squeezing process, the air between the materials is expelled, and the distance between particles reaches a sufficient distance to generate intermolecular forces (such as van der Waals forces, adsorption forces, etc.), thereby forming particle strength.
- The compressed cake material enters the crusher for crushing.
- The crushed material is then sieved by a screening machine to separate granular products that meet the requirements.
- The screened powdered materials may be sent back to the raw material warehouse for secondary rolling to improve the utilization rate of raw materials.
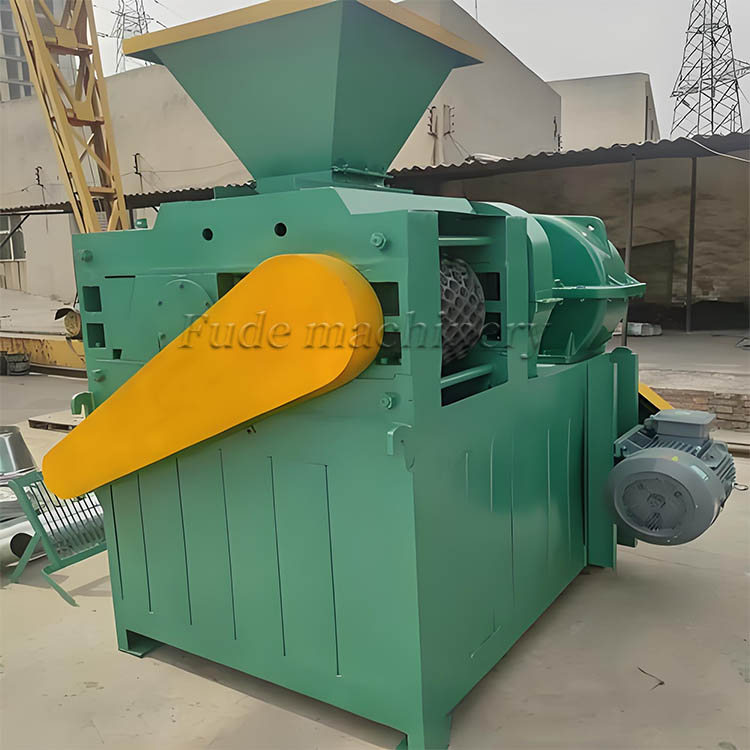
Double roll granulator
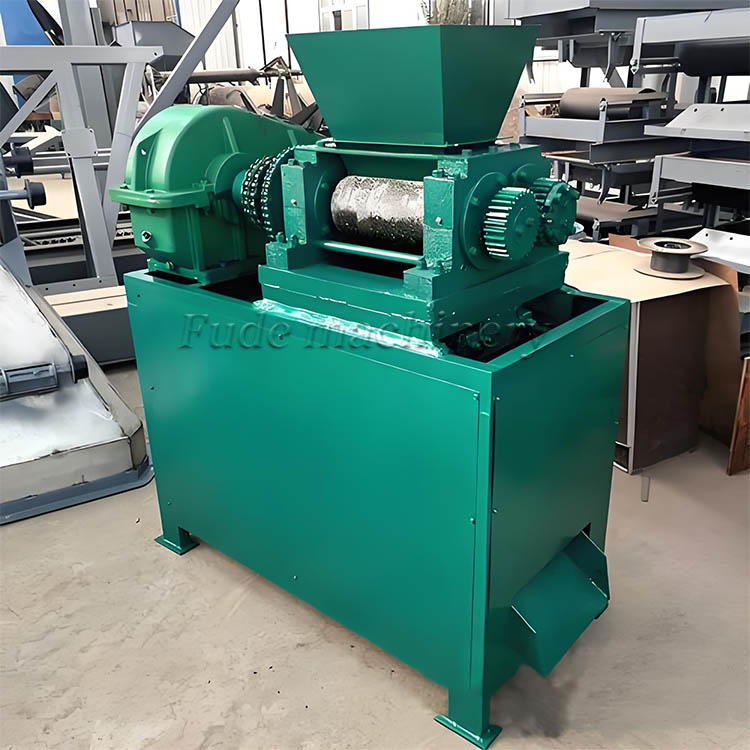
Double roll extrusion granulator
Characteristics and advantages
- Energy saving and consumption reducing: The extrusion granulation process is carried out at room temperature without additional drying measures, which can significantly reduce energy consumption compared to other granulation methods.
- No need for adhesive: granulation is carried out using the intermolecular forces of the material itself, without the need for additional adhesive.
- Wide applicability: Suitable for granulation of various powder materials, such as fertilizers, chemical raw materials, powder materials, etc.
- Stable operation: The device runs stably and reliably, and is easy to maintain.
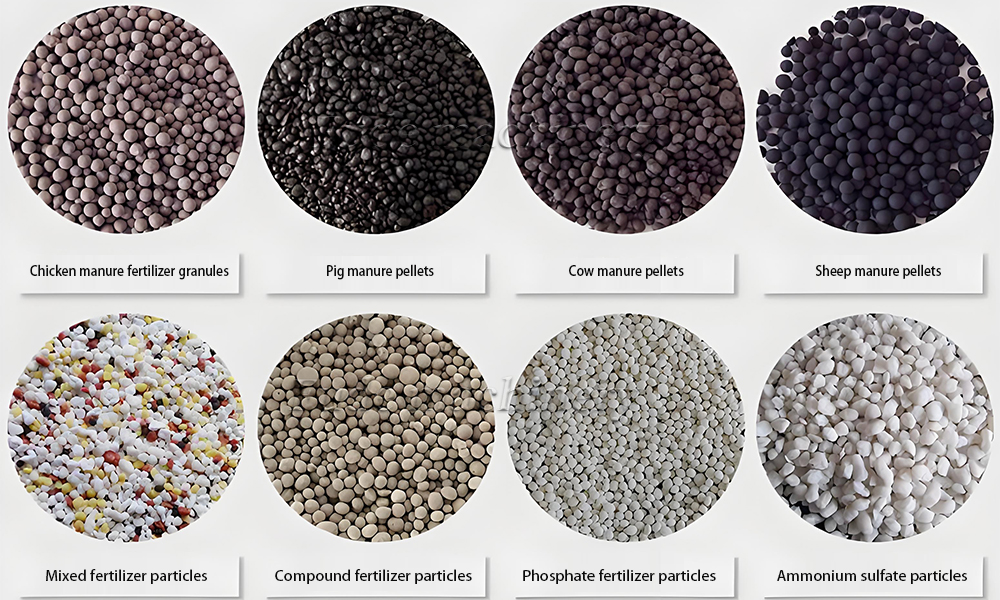
Introduction to Fude Machinery Manufacturer
- The production equipment includes: fermentation raking machine, dryer, granulator, crusher, mixer, round throwing machine, organic fertilizer production line, etc. The company will continue to adhere to the business philosophy of “quality first, customer first” and provide higher quality metal equipment solutions for global customers.
- Since its establishment in 2015, Fude Machinery has been committed to providing high-quality and high-performance wood equipment solutions to global customers. With advanced production technology, strict quality control, and continuous innovative research and development capabilities, we have received customer satisfaction praise.